Valentine Lab post-doc Emma Filippidi makes stronger, stretchier polymers inspired by mussels
Valentine Lab post-doc Emma Filippidi makes stronger, stretchier polymers inspired by mussels
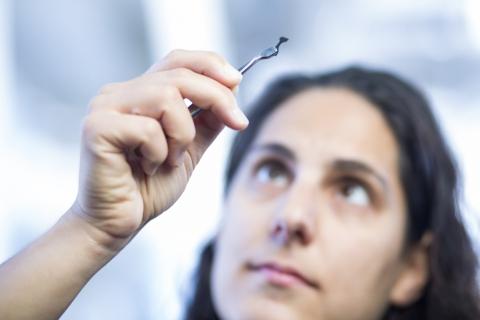
Photo: Emmanouela Filippidi with one of the iron-enriched samples
A marine bivalve inspires researchers to find a new way to make stronger, more stretchy polymers
A wide range of polymer-based materials, from tire rubber and wetsuit neoprene to Lycra clothing and silicone, are elastomers valued for their ability to flex and stretch without breaking and return to their original form.
Making such materials stronger usually means making them more brittle. That’s because, structurally, elastomers are rather shapeless networks of polymer strands — often compared to a bundle of disorganized spaghetti noodles — held together by a few chemical cross-links. Strengthening a polymer requires increasing the density of cross-links between the strands by creating more links. This causes the elastomer’s strands to resist stretching away from each other, giving the material a more organized structure but also making it stiffer and more prone to failure.
Inspired by the tough, flexible polymeric byssal threads that marine mussels use to secure themselves to surfaces in the rugged intertidal zone, a team of researchers affiliated with UC Santa Barbara’s Materials Research Laboratory (MRL) has developed a method for overcoming the inherent trade-off between strength and flexibility in elastomeric polymers. The group’s findings appear in the journal Science.
“In the past decade, we have made tremendous advances in understanding how biological materials maintain strength under loading,” said corresponding author Megan Valentine, an associate professor in UCSB’s Department of Mechanical Engineering. “In this paper, we demonstrate our ability to use that understanding to develop useful manmade materials. This work opens exciting lanes of discovery for many commercial and industrial applications.”
Previous efforts also inspired by the mussel’s cuticle chemistry have been limited to wet, soft systems such as hydrogels. By contrast, the UCSB researchers incorporated the mussel-inspired iron coordination bonds into a dry polymeric system. This is important because such a dry polymer could potentially be substituted for stiff but brittle materials, especially in impact- and torsion-related applications.
“We found that the wet network was 25 times less stiff and broke at five times shorter elongation than a similarly constructed dry network,” explained co-lead author Emmanouela Filippidi, a postdoctoral researcher in the Valentine Lab at UCSB. “That’s an interesting result, but an expected one. What’s really striking is what happened when we compared the dry network before and after adding iron. Not only did it maintain its stretchiness but it also became 800 times stiffer and 100 times tougher in the presence of these reconfigurable iron-catechol bonds. That was unexpected.”
To achieve networks having architecture and performance similar to those of the mussel byssal cuticle, the team synthesized an amorphous, loosely cross-linked epoxy network and then treated it with iron to form dynamic iron-catechol cross-links. In the absence of iron, when one of the covalent cross-links breaks, it is broken forever, because no mechanism for self-healing exists. But when the reversible iron-catechol coordination bonds are present, any of those iron-containing broken cross-links can reform, not necessarily in exactly the same place but nearby, thus maintaining the material’s resiliency even as its strength increases. The material is both stiffer and tougher than similar networks lacking iron-containing coordination bonds.
As the iron-catechol network is stretched, it doesn’t store the energy, so when the tension is released, the material doesn’t bounce back like a rubber band but, rather, dissipates the energy. The material then slowly recovers to reassume its original shape, in much the same way a viscoelastic material such as memory foam does after the pressure on it is released.
“A material having that characteristic, called an ‘energy-dissipative plastic,’ is useful for coatings,” said co-lead author Thomas Cristiani, a UCSB graduate student in the Israelachvili Group. “It would make a great cellphone case because it would absorb a large amount of energy, so the phone would be less likely to break upon impact with the floor and would be protected.”
The dry system the researchers used is important for two reasons. In a wet system, the network absorbs water, causing the polymer chains to stretch, so there is not much extra flexibility left. But with a dry material, the amorphous spaghetti-like strands are initially very compact, with a lot of room to stretch. When the iron cross-links are added to strengthen the polymer, the stretchiness of the dry material is not compromised, because those bonds can break, so the polymer chains are not locked in place. Additionally, removing the water from the network results in the catechol and iron being closer together and able to form regions of high connectivity, which improves the mechanical properties.
“This difference between response in wet and dry systems is huge and makes our approach a game-changer in terms of synthesizing useful engineering materials for high-impact applications,” Valentine said.
She credits the multidisciplinary and deeply collaborative approach of the research team for the project’s success — an endeavor made possible by the Interdisciplinary Research Group on Bio-inspired Wet Adhesion through UCSB’s MRL, a National Science Foundation Materials Research Science and Engineering Center. MRL-affiliated co-authors are Jacob Israelachvili, a professor emeritus in the Materials and the Department of Chemical Engineering at UCSB; Herbert Waite, a professor in UCSB’s Department of Molecular, Cellular, and Developmental Biology; and Claus Eisenbach of the University of Stuttgart, along with Kollbe Ahn, of the campus’s Marine Science Institute.