Giving Fluid Drag the Slip
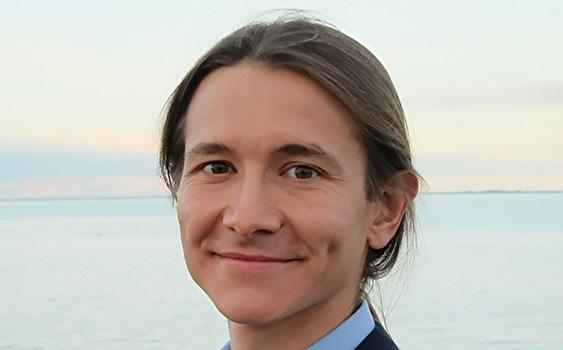
In 2017, UC Santa Barbara mechanical engineer Paolo Luzzatto-Fegizand colleagues published a paper in the Proceedings of the National Academy of Sciences explaining that they had solved a mystery in fluid flow. Now, he has been awarded a prestigious CAREER Award from the National Science Foundation to develop a theory of the phenomenon. In addition, he and UCSB mechanical engineer Frederic Gibou, along with collaborators at the University of Manchester, have received a joint US-UK grant to extend their work to high-speed, turbulent flows.
In that previous research, Luzzatto-Fegiz and colleagues described figuring out why the performance of “superhydrophobic surfaces” (SHS) in the real world did not come anywhere close to matching the performance that paper calculations suggested they should achieve.
SHS are meant to reduce the resistance — known as fluid friction or, simply, drag — that results from water moving along a surface, like the hull of a ship, which would greatly reduce fuel consumption. SHS contain tiny air pockets that separate the hull from the water; because air is much less viscous than water, decreasing the amount of water that comes into contact with the surface decreases drag. At least, in theory.
On paper, SHS are predicted to cut drag by up to ninety percent, but when his team published their 2017 paper, Luzzatto-Fegiz recalls, “People were getting a lot less than that. In fact, they could even get performance that was no better than without the coating.”
Luzzatto-Fegiz and his colleagues figured out that the culprit behind the mysterious failure of SHS were surfactants — compounds, such as soap (but it could be algae, runoff, oils, and many other natural or man-made contaminants) that reduce surface tension. Even trace amounts of surfactants on an SHS, they discovered, could diminish the SHS’s drag-reducing effect.
“Most people who looked at this problem did so from a classical mechanical engineering perspective, so they weren’t aware of the importance of surfactants,” Luzzatto-Fegiz explains. “A few studies had raised the issue, but it was difficult to make the case that surfactants were indeed responsible for the loss of performance.”
In trying to understand the forces affecting performance, Luzzatto-Fegiz and his collaborators became the first to apply simulations to the problem. “That allowed us to see things that people couldn’t see with experiments. What we discovered was that because the interface is so sensitive, the trace surfactant that is already there, even from ostensibly clean water, can be enough to impair drag reduction,” Luzzatto-Fegiz says.
“The surfactants can end up producing drag because of something called the Marangoni effect, which arises from an uneven distribution of surfactant molecules on the interface,” Luzzatto-Fegiz explains. “The cool thing is that the macroscopic effect of drag, which is in the realm of traditional mechanical engineering, is being driven by these microscopic chemical effects.”
Addressing the problem to design effective SHS will require accepting the presence of surfactants, Luzzatto-Fegiz said at the time, “because oceans and rivers contain multitudes of natural and man-made surface-active substances.” They realized it might be possible to “design a way out of the problem” by changing the patterning of the SHS. But a key issue, explains Luzzatto-Fegiz, was the lack of a theory that could be used to understand the experimental results.
“The NSF CAREER award is exciting, because we’ll be able to finally develop a comprehensive theory,” he says. “This is hard, because we not only have the equations for fluid flow, which all mechanical engineers know, but in addition, we have the equations for the transport of surfactants and for how they interact with the surface.”
The theory will be used to design superhydrophobic surfaces that have the best chance of achieving drag reduction in real-world applications.
The NSF CAREER project will focus on laminar flows, whereby each fluid layer moves past neighboring ones with little or no mixing. One application is found in microfluidic systems, such as those used in medical testing. Examples include the tiny systems used to do quick medical diagnostics, which are useful because they require very small volumes of liquid, such as blood, to test a patient, do not require large equipment, and can be done quickly. But such systems have very small channels through which liquid passes. That causes high levels of shear, which, in turn, changes the velocity of the fluid as it passes through, making it hard to control where the particles go, whether red blood cells or something else. “They will tend to distribute in ways very much driven by these velocity patterns, which is often undesirable. If you can reduce the drag on the sides of the channel, you can control the flow,” says Luzzatto-Fegiz, adding, “It is a key application and one of the most common to have been proposed at this point.”
If you can reduce the drag on the sides of the channel, you can control the flow with much greater precision,” says Luzzatto-Fegiz, ensuring that cells, reagents, or dyes will mix or avoid each other as needed.
In addition to using theory, the project will also involve using experiments and simulations to study the performance of SHS having different textures. “They can be like lots of microscopic pillars, or they could resemble long grooves — narrow indentations that are filled with air bubbles,” Luzzatto-Fegiz says. “You can give them any shape you want, as long as you don’t try to make the bubbles too big, which will cause them to collapse, wetting the surface.”
To push the envelope toward faster flows, similar to those around ships, Luzzatto-Fegiz has also teamed up with UCSB’s Frederic Gibou, as well as with mathematicians Julien Landel and Oliver Jensen at the University of Manchester in the UK. Together, they have been awarded a joint grant from NSF and from the UK’s Engineering and Physical Sciences and Research Council (EPSRC), in order to take the first look at the effect of turbulence on this problem.
The NSF-EPSRC project will use a two-pronged approach, combining supercomputer simulations (Gibou’s specialty) and mathematical modeling. The team will implement the first computational algorithm that can simulate the interplay of surfactant and turbulence over a superhydrophobic surface. As Gibou notes, “This will provide a wealth of detailed information about the flow dynamics and the effect of surfactants.”
In addition, the team will develop simpler theoretical models to help predict likely regimes that can maximize drag reduction. “It’s very laborious to run a simulation every time,” says Luzzatto-Fegiz. “A simplified model can save you unbelievable amounts of time, because it can show quickly the parameters that matter and that will be interesting to investigate.”
Getting the textural elements of the SHS to align in a certain way on a large ship will be no easy task. “It’s very difficult to control that, so you have to build into it the understanding that it won’t be uniform, that there will be irregularities; the textures, however shaped, won’t all align exactly,” Luzzatto-Fegiz explains. “Or, if you insist on uniformity, you have to develop a theory to figure out how to do that. There is still this bridge to be built between physics and the application; this is what makes it such an exciting area of research.”